A Treforest business has bounced back from flood devastation by making locally-sourced hand sanitiser and distributing it across the UK – having produced an emergency supply of 20,000 bottles for local frontline staff.
The operation has also resulted in 13 new jobs created thanks to the company’s significant investment in its production line, and has a very small carbon footprint as the entire manufacturing process is completed on site.
Gwalia Healthcare, based at Treforest Industrial Estate, specialises in the manufacture of medical devices and pharmaceutical packaging. It was one of hundreds of businesses severely affected by Storm Dennis just 11 weeks ago – when its manufacturing operation was brought to a halt overnight.
Having re-established or replaced 30% of its manufacturing capability in the six weeks after the floods, Gwalia was able to satisfy 85% of its orders by converting to a 24/7 production operation – prioritising its healthcare, medical and pharmaceutical customers who rely upon it. The Coronavirus outbreak then brought a second unprecedented emergency in quick succession.
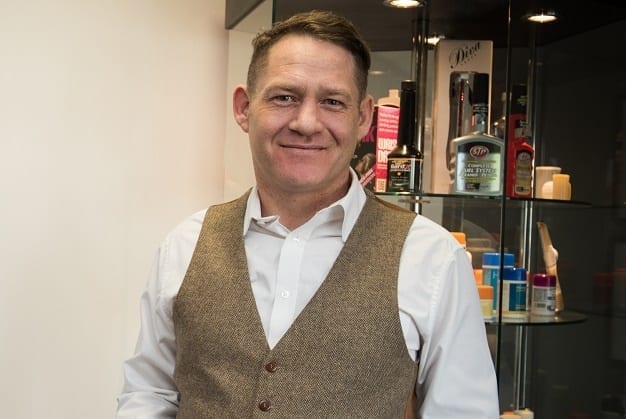
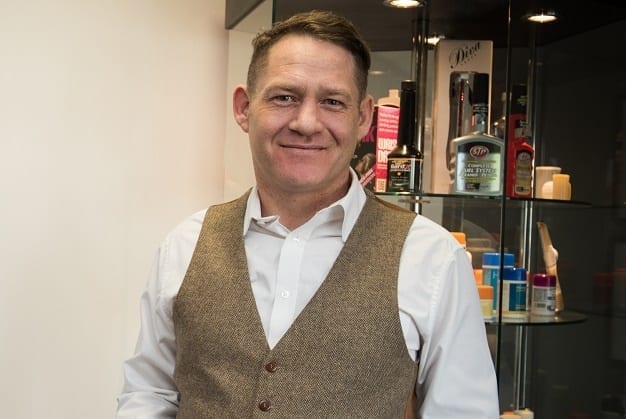
Rod Parker, owner and director of Gwalia Healthcare, said: “It’s been an emotional rollercoaster, having re-established the business after the flooding. We weren’t making hand sanitiser or gel before COVID-19, but we thought as a large number of our industrial customers wouldn’t need their orders from us, why not focus on producing hand sanitiser ourselves?
“We could already make the empty bottles, and could source the gel and alcohol within a 10-mile radius. We had a call from the Council, which needed as much hand sanitiser as we could make for its staff – and we produced 12,000 bottles in that first week as an emergency. That was without a filling line, nor did we have a squeezing dispensing pack for the product.
“We’ve since established a filling line and continue to have lots of enquiries from UK public bodies. We do all of the process in house – from making the product, caps and bottles, to filling and packaging, which gives us an advantage over anyone else doing this.
“The product travels about 15 metres from one machine to another, so there’s no external packaging or storage either – we’re a one-stop-shop. As a result of all of this we can ensure the product has a very low carbon footprint.
“We are in the process of investing £500,000 into our production capability which can supply up to one million bottles of certified gel per week – and this has been the catalyst for creating 13 new jobs, with more to come.”
Councillor Robert Bevan, Rhondda Cynon Taf Council’s Cabinet Member for Enterprise, Development and Housing, added: “Gwalia Healthcare, like many other affected businesses across Rhondda Cynon Taf, deserves huge credit for its response following February’s flooding. The effects of Storm Dennis will be felt for years to come, and it has been followed by a national health emergency which has itself brought many businesses to a standstill.
“The Coronavirus outbreak brought a wide-spread shortage of hand sanitiser, and the Council is very grateful for the support it has received from Rod Parker and Gwalia Healthcare, who have supplied us with 20,000 bottles which we are providing for our frontline and home care staff.”
“Gwalia is a tremendous success story – now mass producing a new product using locally-sourced materials, and providing help for public bodies across the UK. Its product also has a very low carbon footprint as it is produced entirely in-house, and Gwalia’s significant investment into its manufacturing process has created 13 new local jobs to date, which is a huge boost.”
Leave a Reply
View Comments